Knife designs, small seax
It starts with design. Something small, basic, and straight forward.
Layout and estimate material
Punch mark measurements
Preheat material
Tang was isolated using my Hardy Guillotine Tool with rounding dies, then brought down to shape and thickness for initial forging.
The rest of the seax was forged to shape, and taken down to thickness. The spide and tang were measure at 4.5mm as forged, and the edge at 3.5-4mm. The tang edges were also softened slightly.
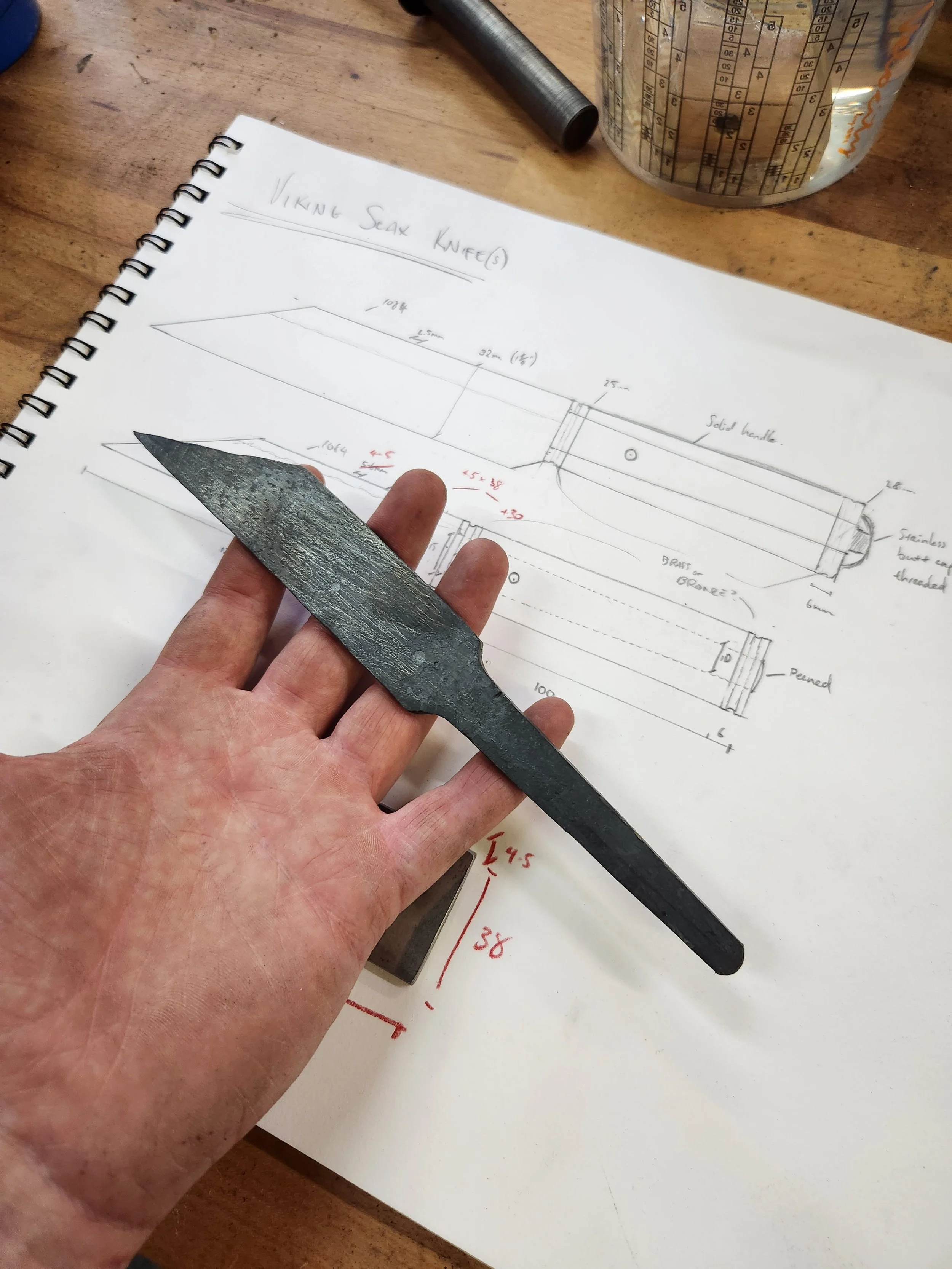

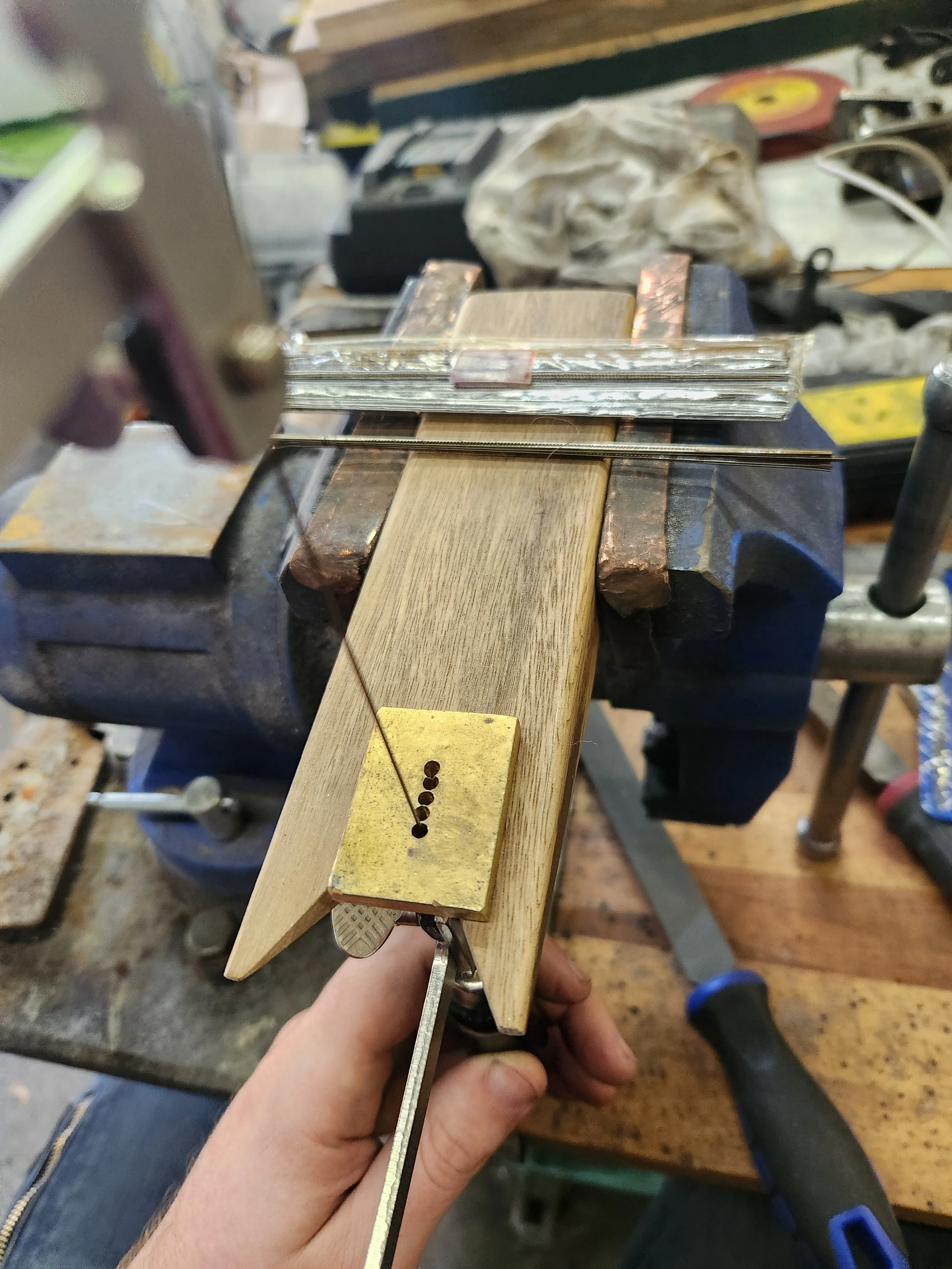

Prior to glue stackup.
Brass, copper, wood handle, copper, brass, steel.
Always check, you never know what you don’t know.
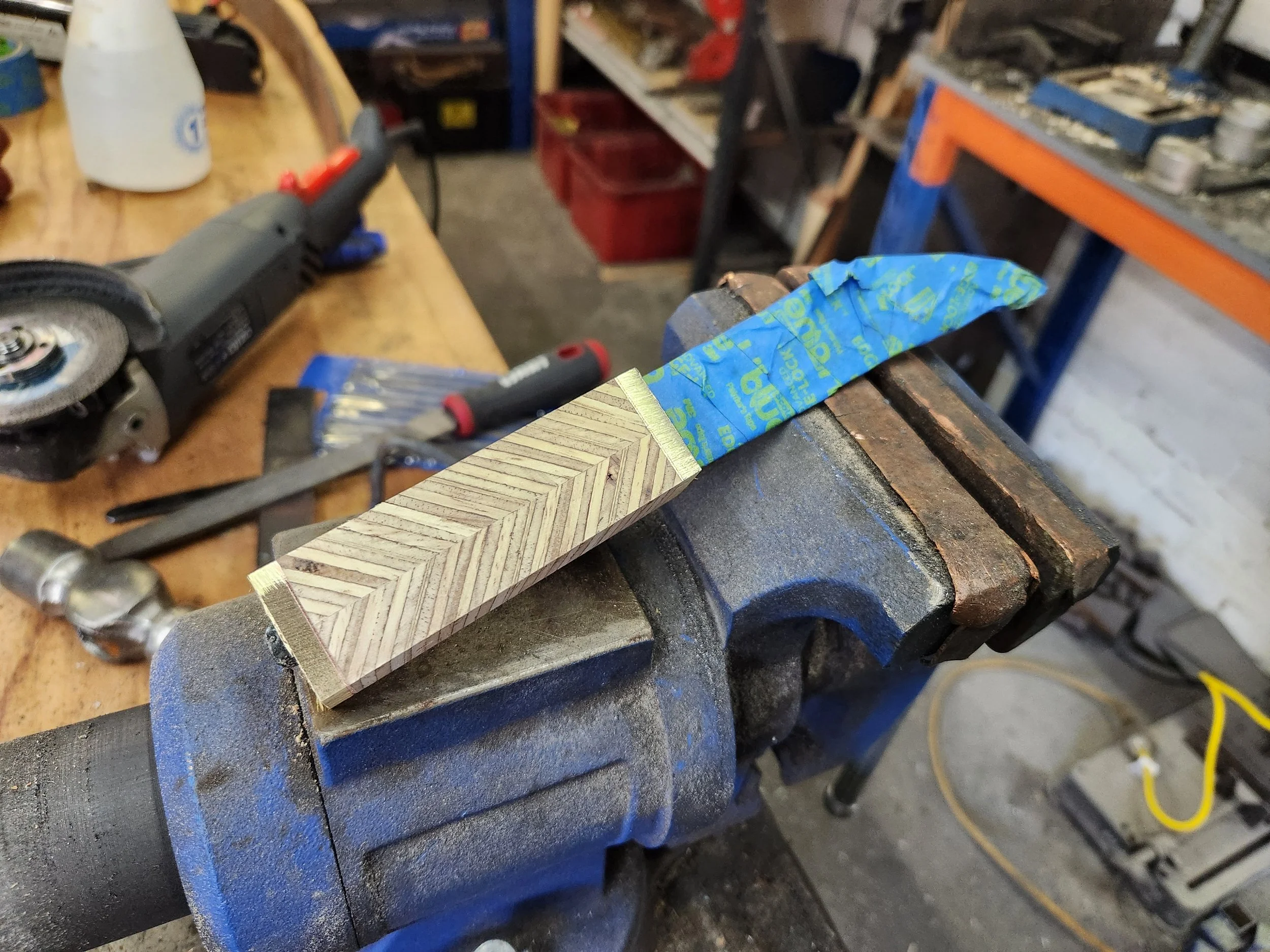




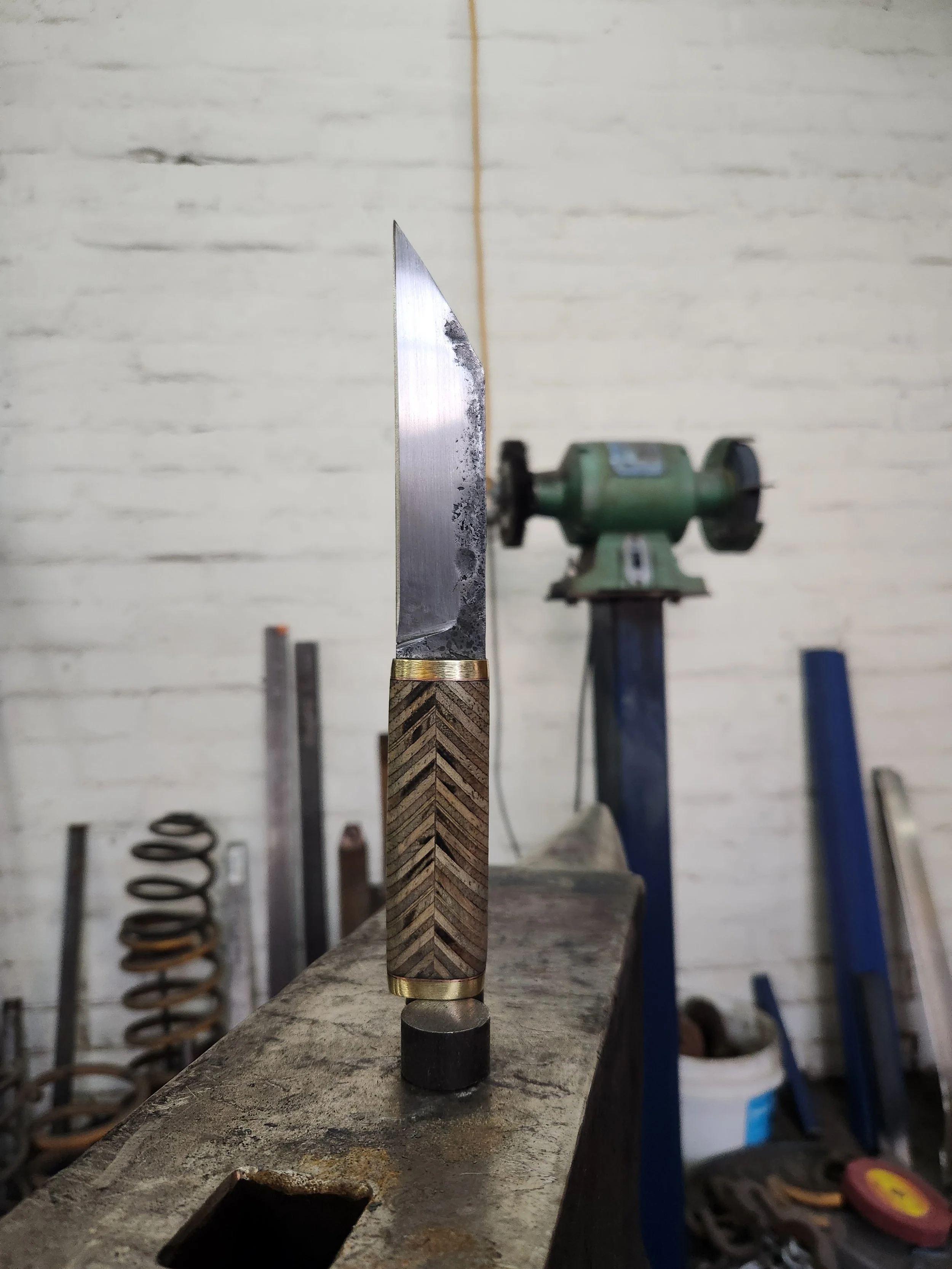

waxed and sharpened.
The knife was sharpened up to 400, and finished with Renaissance Wax on a rag.
Lessons learned?
Sand brass all the way before polish
The softer plywood that the handle is made from darkens and stains easily
Leave more material on the tang and don’t cut it off until the very end
Could forge bevel down further to save material/increase blade width
All in all, an enjoyable process with many lessons learned. I look forward to the next one.